静态扭矩优化之路
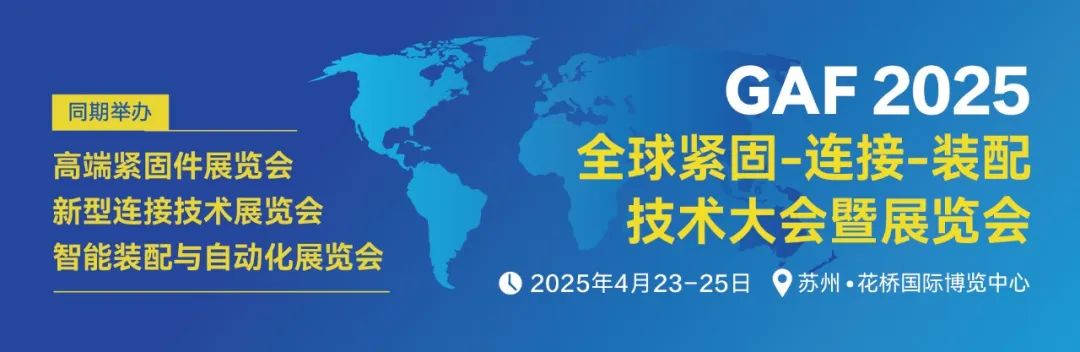
新能源汽车中国已经站在高点,有些车型没有对标产品,无论是整车,还是局部的零部件产品,都需要进行正向开发,这其中静态扭矩就需要一个很好的开发和验证。新车型研发、制造将继续成为各大车企的主要任务之一。
螺栓拧紧扭矩管理一直是总装厂整车制造过程中的重要管理目标,对于量产车而言总装厂主要监管动态扭矩值,通过静态扭矩抽检对拧紧质量进行进一步控制。而对于新车型总装厂对静态扭矩值非常关注,避免因为设计,零部件制造质量问题导致出现很大的扭矩衰减。
静态扭矩值,即装配过程中螺栓首次拧紧后,在短时间内对已拧紧的螺栓扭矩进行检测所得的扭矩值。
螺栓连接的静态扭矩与装配时的动态扭矩一般都不同,能够输出扭矩角度曲线,并能通过一定的算法满足VDI 2645标准中多种检测静态扭矩方法(包含了峰值法、一定旋转角度内的扭矩法、滑动后最小值法、交叉线法、斜率法等5中方法)的静态扭矩检测扳手是总装厂检测新车试装过程中的扭矩拧紧质量的主要工具。
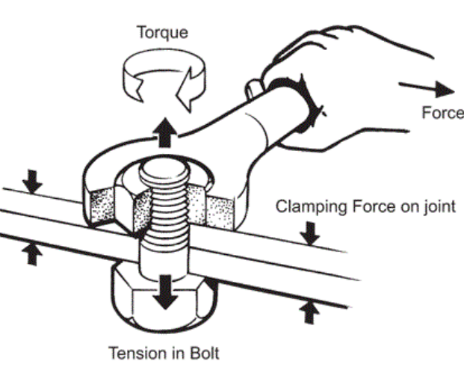
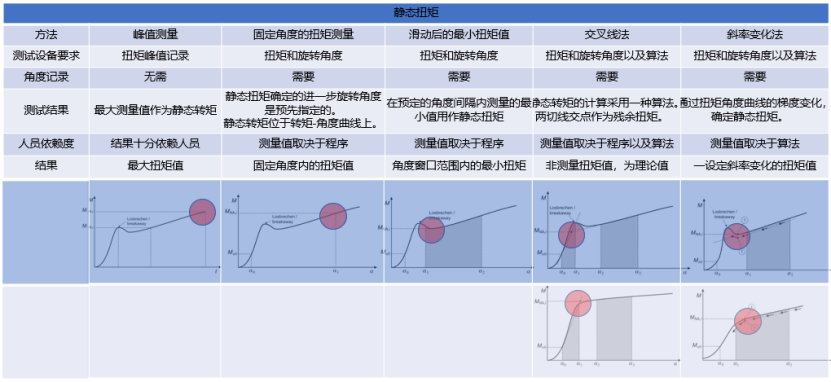

01
小批量试生产静态扭矩标准范围不准确
总装厂对于新车型的试装主要分为样车试生产、小批量试生产、大批量试生产三大阶段。
小批量试生产是总装厂进行新车型试装配的第二大生产阶段,经过多次样车试装,试验验证,基本上可以确定设计没有太大的问题,所有螺栓连接能够满足载荷等功能要求了。
小批量生产阶段,总装厂对新车型的装配工作,不管是从装配人员熟练度、装配工具,还是装配方法方面都有极大的提高,整个装配过程和样车试装阶段都存在极大的不同。所以, 当总装厂进入到新车型的小批量生产阶段时,质检人员在检测整车静态扭矩过程中,往往会发现小批量生产阶段整车关键部位紧固件的扭矩(简称关键扭矩)和重要部位紧固件的扭矩(简称重要扭矩)会出现一个比较常见的问题:部分静态扭矩标准范围设定不当,存在静态扭矩值不合格现象。
静态扭矩标准范围不当的情况主要有三种:
测量值低于下限值
测量值高于上限值
测量值相对偏离上限值或下限值,这也是最常见的情况。
根据螺纹副连接件对扭矩的影响,紧固件的连接类型分为三类:硬连接、软连接、中性连接。
静态扭矩多大范围合适,根据某一次研讨会上面的介绍,不同企业有不同的标准要求,下面列举了大众汽车,通用汽车,福特汽车常见的静态扭矩标准范围要求。这个静态扭矩范围可以作为参考。不管怎么样,静态扭矩的原则应该是保证预紧力要满足一定的要求,也就是螺栓装配后的预紧力要满足载荷要求。
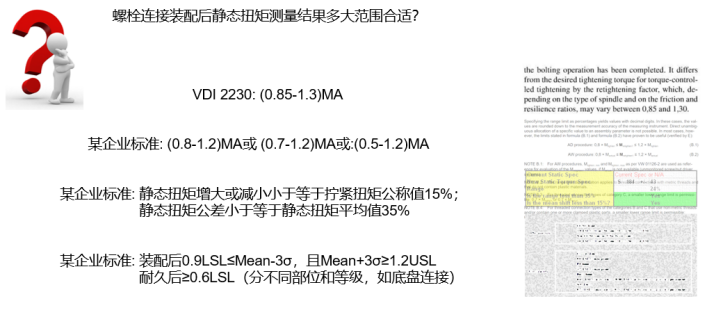
下面,螺丝君分别以某公司某车型制动硬管连接(软连接)、发动机与变速器连 接(硬连接)、燃油箱固定带与车身连接(中性连 接)为例进行以上三种不同类型的螺栓连接类型的静态扭矩分析。
1.1 制动硬管螺栓连接

制动硬管拧紧螺母设计力矩为(18±2)Nm, 制动硬管与制动硬管连接设计确定属于软连接,在样车试制阶段,根据丰田经验算法制定的静态扭矩范围是 11~27 Nm,相当于最大允许衰减39%,最大允许增加50%。

在小批量生产阶段,质检人员通过使用扭矩扳手检 测到的静态扭矩值如下表 所示,所有检测车辆装 配完成后均进行了制动系统气密性检测,检测结 果符合整车制造要求,可以确认测量的力矩均符合制动系统气密性要求。静态扭矩测量结果如下表:
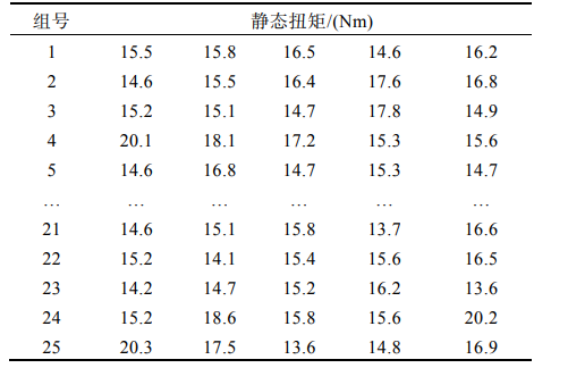
检测的数据一共 125 个,所有数据都符合静态扭矩标准 11~27 Nm,从分布情况看,静态扭矩值相对偏离了静态扭矩标准的上限值,对于总装厂小批量试生产阶段而言,通过经验公式算出的该静态扭矩标准范围存在比实测值上限偏高的问题。
1.2 发动机与变速箱螺栓连接

发动机与变速器连接螺栓设计扭矩为(80± 10)Nm,确定该处为硬连接。发动机与变速器连接属于硬连接,在样车试制阶段,根据丰田静态扭矩经验确定方法制定的静态扭矩范围是 73~111 Nm。
相当于最大允许衰减9%,最大允许增加39%。
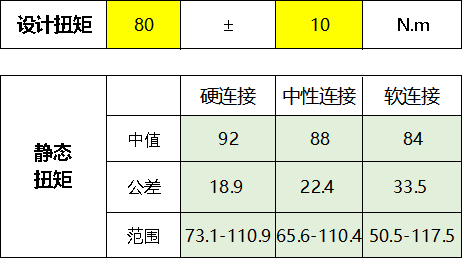
小批量生产阶段,质检人员检测的静态扭矩数据 见下表。
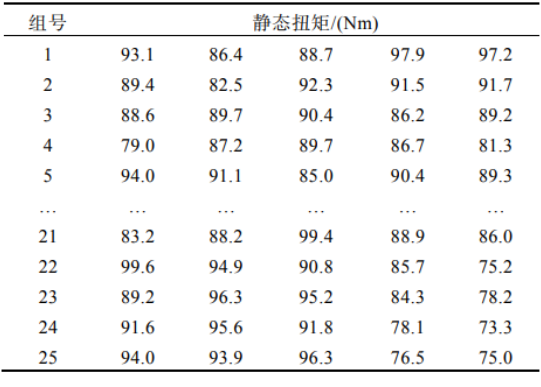
把 125 个检测数据进行分组,从分布情况来 看,静态扭矩标准范围也存在比实测值 上限偏高的问题。
1.3 燃油箱固定带与车身连接

燃油箱固定带与车身连接螺栓设计扭矩为 (40±8)Nm,燃油箱固定带和车身材质都是厚度较薄的钣金件,通过螺栓拧紧后紧固面会出现轻微变形,所以,燃油箱固定带与车身连接属于中性连接,在样车试制阶段,制定的静态扭矩范围 是 31~57 Nm。

相当于最大允许衰减23%,最大允许增加43%。
小批量生产阶段,质检人员检测的静态扭矩数据见下表。

将 125 个检测数据进行分组,从分布情况来看,静态扭矩标准范围存在比实测值下限和上限偏低的问题。
02
原因分析
新车型小批量试生产阶段,总装厂出现部分 静态扭矩标准范围不当的问题,究其原因主要有两个方面:一方面是沿用了样车试生产阶段的经验方法确定出的静 态扭矩标准;一方面是生产条件出现较大变化, 如紧固件紧固工艺、紧固件生产工艺变更。
2.1 静态扭矩沿用样车标准
总装厂样车试生产阶段定义的静态扭矩标准 一般是沿用老车型数据,或者通过经验公式换算而成,因缺乏数据支撑并不精准,为了确保样车试生产的顺利进行,部分静态扭矩标准范围甚至进行了放大,所以当总装厂对新车型的试装进入小批量阶段后,需要对原有静态扭矩标准进行核准。
新车型相对于老车型而言一般都做了大量的设计变更,如改变了紧固件或被紧固件的材料、 表面摩擦系数,有些紧固部位可能增加了防松设 计,如弹簧垫圈、自锁螺母、螺纹锁固胶等,不同的设计变更对静态扭矩的影响程度不一,而这些影响因素并不能通过经验公式换算得出,所以,小批量试生产阶段继续沿用样车阶段的静态扭矩标准势必会对质检工作造成不良影响。总装厂经过多轮样车的试装工作会积累大量的静态扭矩数据,根据测量情况应该对静态扭矩标准范围明显存在问题的地方进行确认、修改。
2.2 紧固件拧紧工艺变更
总装厂新车型试装工作进入小批量阶段后,原有样车试装的纯手工装配模式将无法满足小批量生产节奏,同时,进入小批量生产阶段后,总装厂大部分拧紧设备都应该安装到位,通过小批量试装验证拧紧设备的安装调试情况,以便工艺人员确认新的拧紧设备是否满足总装新车型批量生产的质量要求和节拍要求。
因此,相对于样车生产阶段而言,此时紧固件的拧紧工艺出现了较 大的变化,使用拧紧设备代替原有人工使用动力工具加扭力扳手的装配方式,能有效提高扭矩的控制精度和扭矩的稳定性。
对于静态扭矩值而言, 其数据的波动性也会极大的降低,继续采用原来的静态扭矩标准,就显得标准的范围过大,并不能有效监控拧紧设备的工况,也不利于过程质量的监管。
另外手动工具拧紧速度比较慢,样件生产阶段可以边拧紧边补偿扭矩的衰减,小批量生产阶段采用电动拧紧枪拧紧,转速比较高,扭矩衰减会相应的更大。
2.3 紧固件生产工艺变更
总装厂新车型小批量装配使用的紧固件产品质量会比样车试制阶段装配的紧固件产品质量好很多,主要是因为紧固件的生产工艺出现较大变化。样车试装阶段使用的紧固件量小、紧固件图纸未冻结,此时供应商主要依靠人工和非专用设备生产就能满足总装厂样车试装需求。当总装厂进入小批量装配阶段后,整车零部件图纸基本冻结,紧固件需求数量大,紧固件供应商的生产工 艺也逐步从人工向自动化转变,紧固件表面粗糙度、平面度等参数的稳定性都会得到极大的改善。
同一批次的产品质量差异性会很小,总装在进行试装作业时扭矩的控制精度会的到有效保证,降低了扭矩波动的可能性,所以总装在新车型小批量试装阶段对整车关键紧固部位和重要紧固部位的静态扭矩值能做到更小范围的控制。
03
对策
新车型的设计变更、工艺变更导致了总装厂原有样车试制阶段制定的静态扭矩标准不能适用小批量试装阶段的生产要求,因此必须及时对原 有标准进行调整。
总装厂新车型小批量试装阶段 静态扭矩标准的调整需要结合新车型具体的拧紧部位分析,整车螺纹紧固件装配过程的结果(拧 紧角度/扭矩)可看成一个钟形正态分布的随机变量,基于 6Sigma 理论可知,装配结果数据落在 u± 3δ 的概率应为 99.73%,即意味着每拧紧 10000 个拧紧点才可能有 27 个拧紧点不在[u-3δ,u+3δ] 范围内,此事件为小概率事件。
因此,在样车试装数据的基础上,以均值的正负三个标准差为公差进行修订,修订后的静态扭矩标准,基本覆盖了所有的正常数据,能有效检测和预防异常情况的发生。
以螺丝君上述检测的制动硬管静态扭矩、发动机与变速器紧固扭矩、 燃油箱固定带与车身紧固扭矩为例,根据样车阶段测量情况,通过计算公式可以得出制动硬管、 发动机与变速紧固件的静态扭矩均值、标准差:
均值
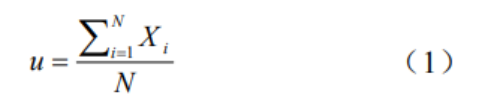
标准差

式中,X1, X2, X3, ..., XN 为测量数据,其平均值为 μ, 标准差为 δ。
3.1 制动硬管连接
经计算可得制动硬管静态扭矩,均值 15.958 4 Nm,标准差 1.509 8 Nm,静态扭矩上限20.487 8 Nm, 静态扭矩下限11.429 Nm。
结合制动硬管检测的 125 个静态扭矩值分布情况来看,最终确定调整为11~21 Nm。
3.2 发动机与变速箱连接
经计算可得发动机与变速紧固件静态扭矩, 均值 90.3 432 Nm,标准差5.692 997 Nm,静态扭矩上限为107.422 Nm,静态扭矩下限为 73.264 Nm。
结合发动机与变速器紧固件静态扭矩值及其分布情况来看,最终确定调整为 73~108 Nm。
3.3 燃油箱固定带与车身连接
经计算可得燃油箱固定带与车身紧固件静态扭矩:均值 47.891 2 Nm,标准差4.977 595 Nm,静态扭矩上限为62.824 Nm,静态扭矩下限为32.958 Nm。
结合燃油箱固定带与车身紧固件静态扭矩值及其 分布情况来看,最终静态扭矩调整为 33~63 Nm。
综上可知,硬连接、软连接、中性连接三种紧固件连接类型的静态扭矩值,均能在拧紧工艺稳定后通过统计分析确定合适的静态扭矩范围。
注意以上统计分析确定静态扭矩范围的前提条件是:
1
制定拧紧工艺的时候就已经确定拧紧后衰减在经验范围内,例如满足大众标准20%的衰减范围内,如果超出该范围需要进行调整拧紧工艺,增加停顿,降速等过程来尽可能降低扭矩衰减;如果仍然衰减较大,就需要设计一起确认衰减这么大是否仍然能够满足要求,最终发布拧紧工艺。
2
测量数据符合正态分布。
3
拧紧扭矩工序能力指数满足1.33以上要求。
只有在这些条件满足的前提下,才可以通过统计分析的方法确定静态扭矩范围。否则,仅仅通过统计分析的方法确定范围就有可能导致本身扭矩衰减太大,也直接通过统计数据确定静态扭矩的范围了。
螺丝君经验与总结
L.S.ENGINEER Experience and Summary
以样车试装阶段检测的静态扭矩数据为基础,首先通过经验算法进行静态扭矩范围的确定。
通过实测静态扭矩值,以均值的 6 个标准差作为公差,统计计算出静态扭矩的上下限,作为最终调整后的静态扭矩范围。
通过这种方法既能有效检测异常扭矩,也能最大限度的避免误报警,同时也为总装后续大批量生产提供技术储备。
今天的话题,就分享到这里,您有任何疑问或建议,或需要进群交流的老铁,可联系下方螺丝君:


+ 螺丝君微信
进紧固连接装配群
10,000+伙伴已加入
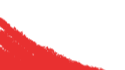
-END-
往期热点
觉得内容有用的话,给螺丝君点个“在看”呗
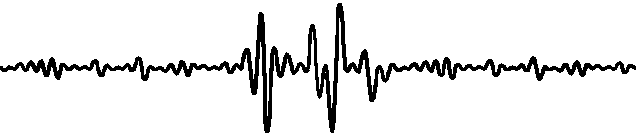